The physical properties of stainless steel castings are higher than those of pig iron, but their forging properties are worse than those of cast iron. Due to the high melting point of stainless steel precision castings, easy air oxidation for desolubilization, poor fluidity of molten steel, and large shrinkage, the volume shrinkage rate is 10-14%, and the line shrinkage is 1.8-2.5%. In order to avoid the shortcomings of stainless steel castings such as insufficient pouring, cold isolation, shrinkage and shrinkage, cracks and slag inclusions, it is necessary to adopt more complicated processing measures than pig iron:
1. Due to the poor fluidity of precipitation, in order to avoid cold insulation and insufficient pouring caused by stainless steel castings, the thickness of stainless steel castings should not be less than 8 mm; the structure of the pouring system software should be simple, and the cross-sectional specifications are larger than those of pig iron; Metal mold casting or hot metal mold casting; moderately increase the pouring temperature, generally 1520 ° ~ 1600 ° C, due to the high pouring temperature, the hydrogen pressure of the molten steel is large, the liquid is maintained for a long time, and the fluidity can be improved. However, if the pouring temperature is too high, it will cause defects such as sturdy crystals, thermal cracks, blowholes and slag inclusions. Therefore, for small and medium-sized, thick-walled and complex-shaped castings, the pouring temperature is about the melting point temperature of steel + 150 °C; the pouring temperature of large and medium-sized and thin-walled castings is higher than its melting point.
2. Because the shrinkage of stainless steel plate precision castings greatly exceeds that of pig iron, in order to avoid the defects of shrinkage and shrinkage of the castings, most of the forging processes use countermeasures such as gate and cold iron and subsidies to achieve sequential condensation.
In addition, in order to avoid the defects of shrinkage, shrinkage, air holes and cracks caused by aluminum alloy die castings, the wall thickness should be uniform, the bevel and bevel structure should be prevented, and sawdust should be added to the sand for metal mold casting. The addition of coke to the core and the selection of hollow cores and oil sand cores can improve the tolerance and air permeability of the sand mold or core.
The specific application of contemporary investment casting methods in industrial production was in the 1940s. At that time, the development trend of airline turbojet engines stipulated the production of heat-resistant alloy parts with complex, high-precision specifications and smooth surfaces, such as leaves, centrifugal impellers, and nozzles. Because the heat-resistant alloy raw materials are difficult to be machined and manufactured, and the parts are so complicated that it is impossible or difficult to manufacture them in other ways, it is necessary to find a new high-precision forming process. Wax casting, after the improvement of raw materials and processing technology, the modern investment casting method has basically obtained a key development trend in ancient times.
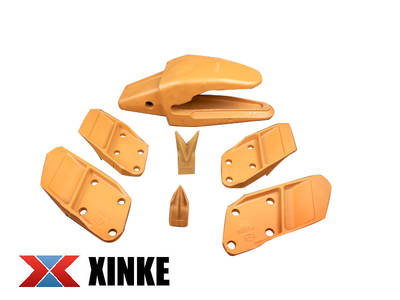
To put it bluntly, the investment casting process is simply to use fusible raw materials (such as wax or plastic) to make a fusible solid model (commonly known as investment mold or solid model), and coat it with several layers of specially made fireproof. Architectural coatings, after drying and hardening to produce a general shell, then use steam or boiling water to melt the solid model from the shell, then place the shell in a sandbox, and fill it with dry sand modeling design. Finally, the metal mold is cast into the calciner and fired at high temperature (for example, when a high-toughness mold is selected, the mold can be fired immediately after being released without modeling design), and the metal mold or the mold is fired. Then, a casting is obtained by pouring the molten metal material therein.
The precision of investment casting specifications is relatively high, generally reaching CT4-6 (CT10~13 for sand casting and CT5~7 for aluminum die casting). There are many factors, such as the shrinkage of the mold material, the deformation of the investment mold, the linear transformation of the shell during the whole process of heating and cooling, the shrinkage rate of the aluminum alloy and the deformation of the casting during the whole process of condensation, etc. Therefore, Although the specification and precision of general investment castings are high, their consistency still needs to be improved (the specification consistency of castings using medium and high temperature waxes should be much improved).
When suppressing the investment mold, a pressing plate with high surface smoothness of the concave mold is selected, so the surface smoothness of the investment mold is also relatively high. In addition, the shell is made of a fire-resistant architectural coating composed of a unique heat-resistant adhesive and a fire-resistant thermal insulation material, which is painted and hung on the investment mold, and the inner surface of the concave mold that is in direct contact with the molten metal material has high smoothness. Therefore, the surface smoothness of investment castings is higher than that of general iron castings, generally reaching Ra.1.6~3.2μm.
The biggest advantage of investment casting is that investment castings have high specification precision and surface smoothness, so it can reduce the machining and manufacturing work, leaving only a small amount of residual processing at a higher position on the part. It is enough, and even some castings only have the capacity of grinding and polishing, and can be used without machining. It is not difficult to see that the selection of investment casting method can save a lot of mechanical equipment and comprehensive production and processing time, and greatly save metal raw materials.
Another advantage of the investment casting method is that it can forge complex castings of various aluminum alloys, and is very capable of forging heat-resistant alloy castings. For example, the leaves of a jet-style diesel engine have a streamlined outer contour and an inner wall for refrigeration that are basically impossible to produce by machining. Manufacturing with investment casting can not only ensure mass production, but also ensure the consistency of castings, and prevent the stress of residual knife lines after machining.
Fenghua Xinke Precision Casting Co., Ltd is a enterprise specializing in the manufacturing of Silica Sol Castings,Lost Wax Investment Castings,Coated Sand Castings and finished products in stainless steel,carbon steel and low alloy steel. Our company is a world class manufacturer and supplier of investment castings with silica sol or water glass process in China. We both have our own steel casting foundry and CNC machining factory,which enable us to supply both precision castings and finished products with an annual production capacity of over 20,000 tons. As OEM Agricultural Casting Manufacturers and Custom Construction Machinery Casting Factory, our products cover a wide range of industries including train & railway, automobile & truck, construction machinery, mining machinery, forklift, agricultural machinery, shipbuilding, petroleum machinery, construction, valve and pumps, electric machine ,hardware, power equipment and so on.